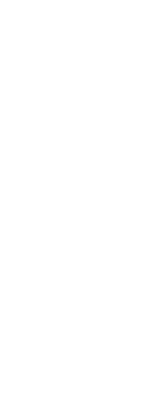
The twelve cavernous, vaulted chambers underneath the Leigh Woods Tower are festooned with fragile stalactites which can occasionally fall from the ceiling, smashing into fragments as they land. Once they have fallen, there is no way to put them back – so they are collected by our guiding teams and passed around during Hard Hat Tours so visitors can examine them more closely and see their inner structure – usually long and thin and hollow like a drinking straw.
The stalactites grow when rainwater seeps through the lime mortar used to construct the huge abutment. Often when stalactites form in natural caves and manmade structures the dominant mineral in the deposit is calcite, otherwise known as calcium carbonate. Although the Clifton Suspension Bridge Trust had never tested the chemical composition of our stalactites, it seemed likely that it would also be true in this case: many structures built at this time used Portland cement, which is usually made with limestone, and the Avon Gorge would have provided in abundance!
When we learned that calcium carbonate is also a key ingredient used by potters to create glaze, we thought this provided an ideal opportunity for some creative experimentation! Visual Artist Phil Root was ideally placed to help us: he uses ceramics to explore human relationships to dwelling, landscape and the earth and was already running workshops in the city on local clay and glaze development. Phil guided us through the process of glaze theory, ably assisted by ceramics student, Karis Bouher.
The stalactite was baked in the kiln to remove water and burn off impurities. During this process, the layers in the stalactite separated and afterward it appeared flaky, crumbling easily to powder when touched.
Using a pestle and mortar, the stalactite was ground to a powder . This had to to be done inside an extraction chamber and wearing a breathing mask to prevent inhalation.
Glaze has four main ingredients, so there was more preparation to be done. For this experiment we used
- Potash (potassium). The potash acts as a flux to lower the melting point of the materials when mixed.
- Quartz – otherwise known as silica. This is he ingredient that provides glaze with its glassy finish. Quartz also prevents the glaze from cracking as it cools to create a uniform surface.
- Clay – Phil used a tried and tested local clay. Clay stabilises the mixture and stops the glaze from melting off the object it’s meant to be covering.
- Calcium carbonate – our stalactite. This also helps to stabilise the clay and prevent it from running.
Phil and Karis also added two more ingredients to the mix in order to create an interesting finish:
- Rutile – or crystals of titanium dioxide. Rutile is used to add speckles, streaks or mottled effects to glazes.
- Cobalt. An oxide which produces blue colouring in glazes.
It is important to find the best combination of ingredients before mixing a large quantity of glaze as there is no certainty as to the end result. Karis took on the job of measuring and mathematics, combining different percentages of the raw ingredients to create a test palette. Once the palette was fired, we could see that not all the mixes had been successful. Three of the most appealing glazes were selected to be mixed in larger quantities.
To complete the project, nine hexagonal tiles were cut and decorated with different patterns and textures. They were left to dry, then bisque fired. This first firing makes the clay porous and strong enough to handle, and prevents objects disintegrating when glaze is applied.
The three glazes were mixed in larger quantities and applied in single and double coats to the hexagonal tiles. Once they had dried, the tiles were glaze fired to create the final result. The experiment was a success! Three glazes; one without any additional colourings; and two with both rutile and cobalt were created from the stalactite. As the glaze was applied thickly, not all of the glazes were perfectly smooth – but we’re still pleased with the results!